What is Porosity in Welding: Usual Sources and Reliable Treatments
What is Porosity in Welding: Usual Sources and Reliable Treatments
Blog Article
Porosity in Welding: Identifying Common Issues and Implementing Best Practices for Prevention
Porosity in welding is a prevalent issue that usually goes unnoticed till it triggers substantial problems with the honesty of welds. This common defect can jeopardize the stamina and sturdiness of bonded frameworks, posing safety dangers and leading to pricey rework. By recognizing the source of porosity and executing reliable prevention strategies, welders can substantially enhance the top quality and integrity of their welds. In this conversation, we will discover the crucial aspects adding to porosity formation, examine its destructive results on weld efficiency, and talk about the most effective techniques that can be taken on to decrease porosity event in welding procedures.
Common Reasons of Porosity
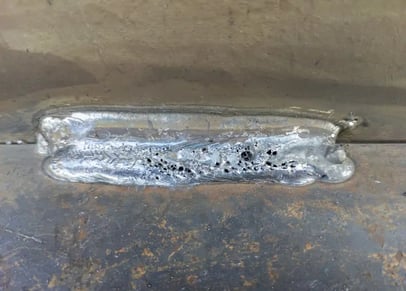
Making use of unclean or wet filler materials can introduce pollutants right into the weld, adding to porosity problems. To mitigate these usual reasons of porosity, detailed cleansing of base steels, proper securing gas choice, and adherence to optimum welding criteria are necessary practices in achieving top quality, porosity-free welds.
Influence of Porosity on Weld Quality

The existence of porosity in welding can significantly jeopardize the architectural integrity and mechanical residential or commercial properties of welded joints. Porosity creates voids within the weld steel, deteriorating its general strength and load-bearing capability.
Welds with high porosity degrees tend to display reduced effect toughness and lowered capability to flaw plastically prior to fracturing. Porosity can hinder the weld's capability to properly send pressures, leading to early weld failing and possible safety dangers in essential structures.
Best Practices for Porosity Avoidance
To boost the architectural honesty and high quality of welded joints, what particular procedures can be carried out to decrease the event of porosity during the welding procedure? Making use of the right welding strategy for the certain material being bonded, such as changing the welding angle and gun position, can better protect against porosity. Routine examination of welds and immediate remediation of any type of problems recognized during the welding process are crucial practices to avoid porosity and produce top notch welds.
Value of Proper Welding Strategies
Carrying out correct welding strategies is critical in making sure the architectural honesty and quality of welded joints, constructing upon the structure of reliable porosity avoidance procedures. Excessive warmth can lead to increased porosity due to the entrapment of gases in the read here weld pool. Furthermore, using the ideal welding specifications, such as voltage, current, and take a trip speed, is vital for accomplishing audio welds with minimal porosity.
Furthermore, the selection of welding procedure, whether it be MIG, TIG, or stick welding, must line up with the particular demands of the project to make certain ideal outcomes. Proper cleansing and preparation of the base steel, in addition to choosing the ideal filler material, are additionally necessary components of skillful welding strategies. By adhering to these ideal techniques, welders can lessen the risk of porosity development and create top quality, structurally my explanation audio welds.

Checking and Quality Assurance Measures
Quality assurance steps play a crucial function in verifying the honesty and reliability of bonded joints. Checking treatments are vital to spot and stop porosity in welding, ensuring the stamina and durability of the final product. Non-destructive testing methods such as ultrasonic testing, radiographic screening, and visual assessment are frequently employed to determine prospective defects like porosity. These techniques permit the analysis of weld high quality without compromising the stability of the joint. What is Porosity.
Conducting pre-weld and post-weld evaluations is also essential in keeping quality assurance criteria. Pre-weld examinations include confirming the materials, tools settings, and cleanliness of the job area to prevent contamination. Post-weld examinations, on the various other hand, assess the final weld for any type of problems, including porosity, and confirm that it satisfies defined criteria. Executing an extensive quality control strategy that includes comprehensive testing treatments and examinations is check this site out vital to reducing porosity concerns and guaranteeing the total top quality of welded joints.
Verdict
Finally, porosity in welding can be an usual issue that affects the top quality of welds. By determining the usual reasons for porosity and applying best practices for avoidance, such as correct welding methods and testing procedures, welders can make certain premium quality and trusted welds. It is vital to focus on prevention approaches to decrease the occurrence of porosity and keep the stability of welded structures.
Report this page